|
|
|
|
Once
upon a time there were some pieces of wood... Paraphrasing
Carlo Collodi you maight start in such a way the story
of a violin making but also of a viola rather than
a cello. In a certain sense, a reference to the fairytale
of Pinocchio can be fitting if you think about the
final result deriving from working the raw wood when
the able hands of the craftsman put his just completed
work into the same expert hands of a musician. A real
magic seems to be happened.
The concerned pieces of wood
are not ordinary pieces of wood. Their names sound
like titles:
"Spruce from Val di
Fiemme"
"Balkan Mountainous
Maple"
"Black Ebony from Madagascar"
That's quite enough to get
impressed facing such a blazon!
|
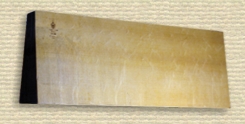 |
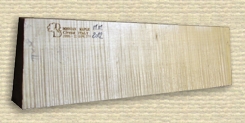 |
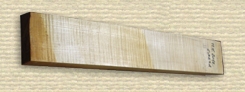 |
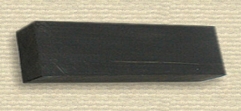 |
Actually, the black ebony
from Madagascar would be really the best for a luthier.
But, on the other hand, it is not easy to get it,
so the most common ebony from Africa is really the
most used.
Now,
let's have a brief look on how a violin, the symbol
of the string instruments by definition, is made according
to the canons of classical violin making. The pictures
below may help to do that by highlighting the main
components of the instrument.
|
First
of all we should watch two components in particular:
those ones having not so obvious a specific functionality
unlike the others. These components are the "bass
bar" and the "sound post".
|
The
bass bar is a strip of fir wood appropriately shaped
placed under the soundboard parallel to the strings
in correspondence of the thicker low tone ones (third
and fourth). These ones, through the left foot of the
bridge, exert a considerable force on the board itself
and so the most evident function is that of a reinforcement
of the structure. Moreover, it also spreads low tone
strings vibrations across the soundboard. |
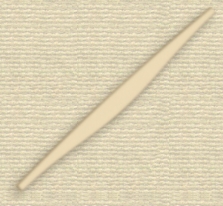 |
In a similar way the sound
post, a small fir cylinder interlocking between the
soundboard and the back and symmetrically positioned
to the bass bar near the right foot of the bridge, performs
two functions: the main one is acoustic since it transmits
vibrations from the soundboard to the back of the instrument
allowing the resonance of the whole sound box; the other
function, like for the bass bar, is spreading the force
exerted on the soundboard by the strings unloading it
to the back. |
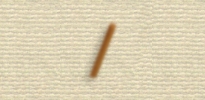 |
The acoustic success or failure of the whole instrument
may depend on a more or less positioning of these
components by the luthier to confirm that very often
what you can't see is what makes the difference. It
means mastery of technique acquired after years of
intense learning and enthusiastic experimentation.
|
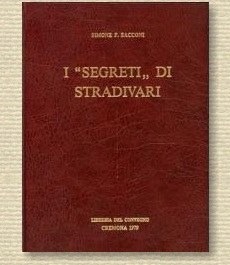 |
Marco Cioni who, since
he was a teenager, called himself "aggeggione",
a Tuscan term identifying a person who knows no statements
such as "I cannot", "I am not able"
because he tries and tries until he succeeds, found
many writings by ancient master luthiers around the
world, such as Domenico Angeloni, Simone F. Sacconi,
Antoine Vidal and, judging by the results, he studied
them very carefully.
He says: "To make my first violins I followed
the directions stated in the book "The Secrets
of Stradivari" by S. Sacconi. As a first result
I got a too small violin of 34 cm and a half. The
second one turned out to be too large, just over 36
cm".
Well, things happen you would say.... if you think
that the standard size is 35.6 cm ...!
Now, after more than ten years of learning and experience,
Marco makes string instruments by manufacturing one
by one all the necessary parts and using woods of
the classical tradition but not only.
"A string quartet (typical set of a luthier's
manufacture which consists in a viola, a cello and
two violins) should be get from wood taken from the
same plant", explains Marco. "Usually I
employ traditional wood but sometimes I like to experiment".
And he continues: "To make the linings, for instance,
I use a timber that spontaneously grows in Torbecchia
(the place where he lives). My uncle, a carpenter,
used to call it Salia but it is a type of willow,
actually. Even Stradivari sometimes used the willow",
he smugly says. Marco continues: "Even here,
around the house, it grows another type of plant that
surprisingly revealed unexpected acoustic qualities:
the Robinia or Locust-tree. I have a client, a friend
of mine as well, who is a concertmaster of the Sanremo
Symphonic Orchestra", he says with a touch of
pride, "that honored me by testing my instruments.
He really likes this wood, as he has pointed out more
than once.
One of the first times I used that wood, I remember
I had prepared a tailpiece made with Robinia and sent
it to him by mail without any particular expectation,
actually. Well, he phoned me, surprised by the peculiar
characterization of the sound achieved using that
tailpiece". A great satisfaction, let's face
it!
|
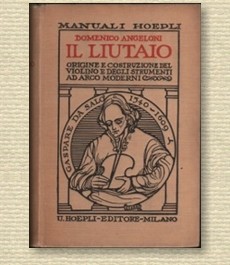 |
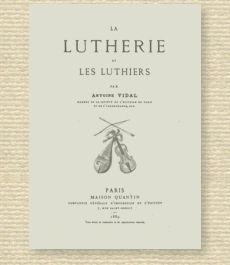 |
|
Here
is one of Marco's instruments made with some no traditional
wooden components. It is a violin, a part of a string
quartet. The chinrest is made with Robinia; tailpin,
tailpiece and pegs are made with Erica, another kind
of wood revealing interesting acoustic qualities.
Another particular feature concerns the upper nut. In
this case wood is not used (usually ebony is used as
well as for the lower nut). In fact it is obtained by
an ox bone which is previously treated with sodium hydroxide
(caustic soda) and boiling water. It is not so unusual
to find some instruments from Marco's manufacture showing
both upper and lower nuts made of this material. Some
examples of this are given by the violins displayed
further on in this section.
Furthermore note also the gold trim on the pegs and
the inlay on the fingerboard made of gold as well and
showing the Author's brand name. |
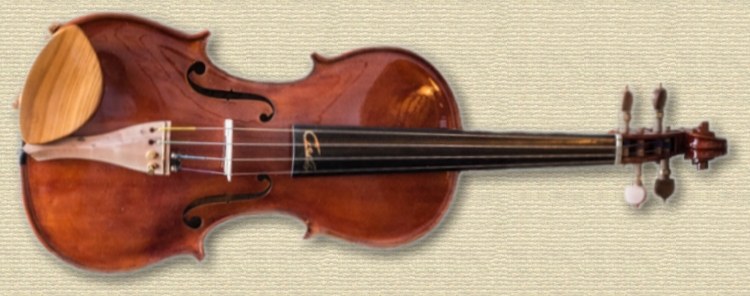 |
From
the beginning of his apprenticeship Marco kept a diary
of his own experiences like an explorer in distant lands
that minutely updates his travel notebook at every rest.
With the patience of an amanuensis monk, Marco wrote
down everything in great detail and accurate pictures,
everything in a calligraphy as they used in the past.
|
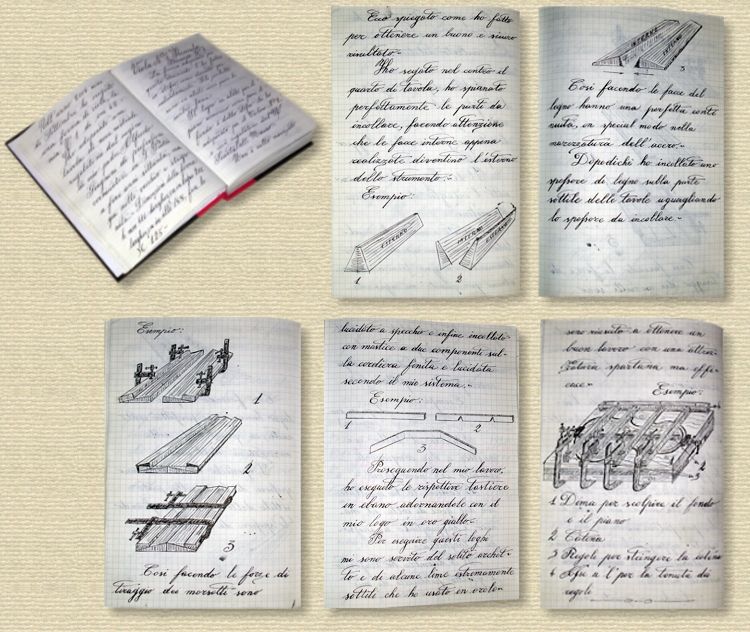 |
Marco
slowly does all this just for pure passion, in the quiet
of his laboratory. Free of constraint and deadlines
of any kind he does not use semi-finished parts but,
as already mentioned, he makes his own everything he
needs. |
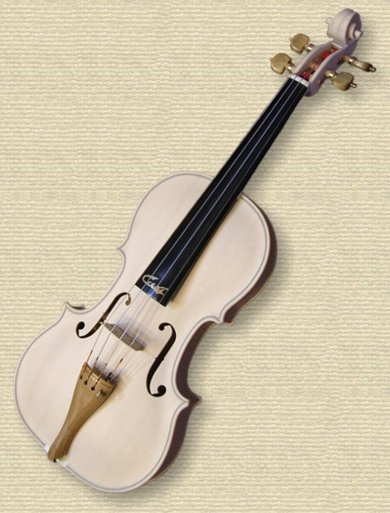 |
To complete the real violin making manufacturing
process, that is, bringing the violin into a state
called "in pajamas", as the jargon has it,
- which means unpainted - , it may takes until a month.
The adjoining photo shows just a "still-to-be-dressed-up"
violin, a procedure that, we must not forget, may
take even a longer time.
Note that Marco spends part of his time also to convey
his art to other people. It is not so unusual, if
you come to his lab, to find him chiseling a soundboard
and, at the same time, keeping up with one or more
apprentices who get the teachings of the master.
It is Marco that tirelessly strives to show them the
various techniques, wood modelling, natural glue preparation,component
assembling and finishing operations.
In the pictures on the side and below we can see Marco
teaching Alessandro how to remove the internal shape
on which ribs and linings have been assembled after
they have been glued to the back of the violin.
Afterwards, the squareness of the blocks to the horizontal
plane is checked.
|
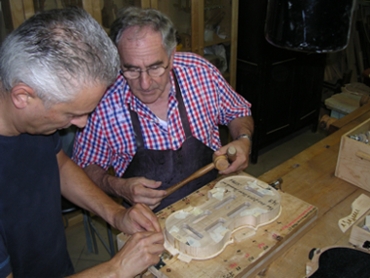 |
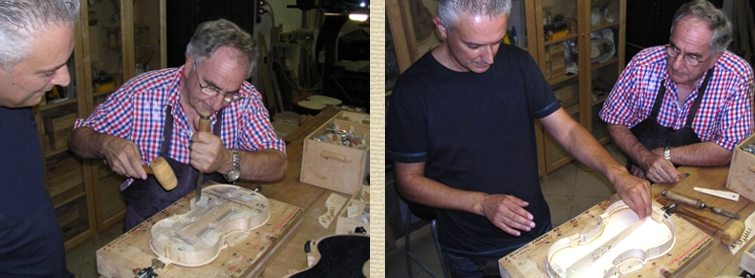 |
At
the end of this section let's get back for a while to
the Robinia wood so that we can speak about a sort of
"experiment" that Marco successfully completed
some time ago and that made him assume, at that time,
the role of heretic - metaphorically speaking - against
the orthodoxy of violin making. |
As mentioned above, Marco
gets the Robinia wood around his house. Many years ago,
a significant number of cut down plants were abandoned
on the ground. He says: "There were several huge
nearly century-old trees torn down and left in the woods.
They had never been cut to make firewood. About ten
years ago I collected those trunks which, in the meantime,
had lost bark and sapwood, devoured by termites and
elements. I had some of those logs sawed to tables,
continues Marco, "to make a cutting board".
For more information about the peculiarity of this cutting
board, click on the image at right to directly read
from Marco's notebook. |
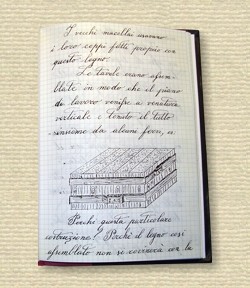 |
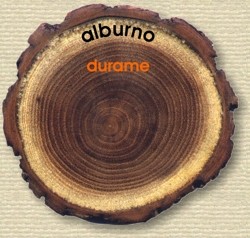 |
After
discovering again this "essence", - like a
tree species and the wood you can get are defined within
forestry -, Marco began manufacturing some tailpieces
made of Robinia with excellent results. Among them,
regarding one in particular, we have already talked
about. It was a really short step from there to find
himself wondering why not to manufacture a violin that
were almost completely made in Robinia. Said and done! |
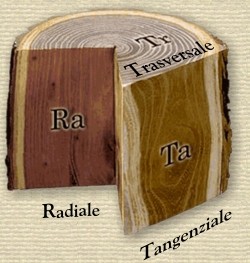 |
From
one of the best preserved logs, with a tangential cut
from the trunk area known as "heartwood" but
however as close as possible to the rind or bark, Marco
got the necessary pieces for the back, ribs and neck
of the violin. Even the tailpiece, chinrest and pegs
were made using the Robinia but, like the different
color of them suggests, they were got from a different
log. On the other hand, Marco used some willow wood
for linings and blocks. Finally he used, with a certain
relief for purists, the classic spruce wood for the
soundboard, sound post and bass bar.
The result is the instrument you can see in the pictures
below. Those who tested it say that you only need to
lightly touch the strings to realize that this violin
has an excellent music performance.
Congratulations, Marco! |
|
|
 |
|
|
|
|